Plaster is a versatile material used in various art forms, including printmaking. Creating a plaster for printmaking involves mixing plaster powder with water to form a smooth paste that is then applied to a surface and allowed to dry. This dried plaster surface can then be used as a printing matrix, creating unique and textured prints.
Plaster has been employed in printmaking for centuries, valued for its ability to capture intricate details and produce high-quality prints. It is particularly suitable for intaglio printing techniques, where the design is etched or engraved into the plaster surface and then inked and printed. Plaster’s durability and ability to hold fine lines make it an ideal choice for creating detailed and expressive prints.
To make a plaster for printmaking, you will need plaster powder, water, a mixing container, and a surface to apply the plaster to. The ratio of plaster powder to water can vary depending on the desired consistency, but a good starting point is a 2:1 ratio of plaster to water by volume. Gradually add water to the plaster powder while mixing thoroughly until a smooth and lump-free paste is formed. The plaster should be thick enough to hold its shape when applied but not too thick that it becomes difficult to spread.
How to Make a Plaster for Printmaking
Creating a plaster for printmaking involves several essential aspects, each contributing to the successful production of high-quality prints. These key aspects encompass the preparation of materials, the mixing and application of the plaster, and the drying and preparation of the plaster surface for printing.
- Materials: The selection of appropriate plaster powder and water is crucial for creating a durable and workable plaster.
- Mixing: The ratio of plaster powder to water and the thoroughness of mixing directly influence the consistency and quality of the plaster.
- Application: The method of applying the plaster to the surface, whether pouring, spreading, or sculpting, affects the final texture and thickness of the plaster.
- Drying: The drying time and conditions impact the strength and stability of the plaster.
- Surface preparation: The plaster surface may require sanding or other treatments to achieve the desired smoothness and receptiveness to printing.
- Printing: The choice of printing technique, such as intaglio or relief, determines the specific requirements for the plaster surface.
These key aspects are interconnected and influence the overall outcome of the printmaking process. By carefully considering each aspect, printmakers can create plasters that meet their specific artistic needs and produce high-quality, visually striking prints.
Materials
In the context of printmaking, the selection of appropriate plaster powder and water is a critical aspect of creating a durable and workable plaster. The quality of the plaster directly influences the success of the printmaking process, as it serves as the foundation for the printed image. Several factors contribute to the importance of selecting the right materials:
- Durability: The plaster must be strong enough to withstand the pressure of printing, which involves applying pressure to transfer the inked design onto paper or other materials. Poor-quality plaster may crack or crumble under pressure, ruining the print.
- Workability: The plaster should be easy to mix and apply, allowing the printmaker to achieve the desired consistency and thickness. Unworkable plaster can be difficult to spread evenly, leading to an uneven surface that affects the quality of the print.
- Texture: The texture of the plaster can impact the final appearance of the print. Different types of plaster powder can produce different textures, from smooth to grainy. The choice of plaster powder should align with the desired aesthetic outcome.
Therefore, carefully selecting the appropriate plaster powder and water is essential for creating a durable, workable, and visually appealing plaster that meets the specific requirements of the printmaking process.
Mixing
In the context of “how to make a plaster for printmaking”, the mixing process is a critical step that directly affects the consistency and quality of the plaster. The ratio of plaster powder to water determines the thickness and workability of the plaster, while thorough mixing ensures a smooth and lump-free consistency. Both factors contribute to the overall success of the printmaking process.
The correct ratio of plaster powder to water is essential to achieve the desired consistency. If the ratio is incorrect, the plaster may be too thick or too thin, making it difficult to apply evenly and affecting the quality of the print. Thorough mixing is equally important, as any lumps or undissolved plaster particles can create imperfections in the plaster surface, which will be transferred to the print.
Understanding the importance of mixing and the proper ratio of plaster powder to water empowers printmakers to create plasters that meet their specific artistic needs. By carefully controlling these factors, they can achieve consistent results and produce high-quality prints with sharp details and rich textures.
Application
In the context of “how to make a plaster for printmaking”, the application of the plaster plays a significant role in determining the final texture and thickness of the plaster, which in turn affects the quality of the print. The method of application can be tailored to achieve specific artistic effects and meet the requirements of the printmaking technique.
- Pouring: Pouring the plaster onto a flat surface creates a smooth and even layer. This method is suitable for creating a uniform printing surface with consistent thickness, which is ideal for techniques like intaglio or relief printing.
- Spreading: Spreading the plaster using a trowel or spatula allows for more control over the thickness and texture of the plaster. This method can create variations in the surface, adding depth and texture to the print. It is often used in collagraph or monoprinting techniques.
- Sculpting: Sculpting the plaster involves shaping the plaster while it is still wet, using tools or hands. This method provides the most artistic freedom and allows printmakers to create unique and highly textured surfaces. It is commonly used in sculptural printmaking or experimental printmaking techniques.
Drying
Proper drying is a crucial step in the process of making a plaster for printmaking, as it directly affects the strength and stability of the plaster. The drying time and conditions must be carefully controlled to ensure that the plaster dries evenly and without cracking or warping. If the drying process is rushed or uneven, the plaster may become weak and brittle, compromising the quality of the printmaking process.
The ideal drying time for plaster can vary depending on the thickness of the plaster layer, the ambient temperature, and the humidity level. Generally, thicker layers of plaster will require longer drying times. It is important to allow the plaster to dry completely before proceeding with the printmaking process, as any remaining moisture can affect the adhesion of the ink and the overall quality of the print.
In addition to the drying time, the conditions in which the plaster dries are also important. The plaster should be dried in a well-ventilated area with a consistent temperature. Avoid exposing the plaster to direct sunlight or heat sources, as this can cause the plaster to dry too quickly and increase the risk of cracking.
Understanding the importance of proper drying and adhering to the recommended drying time and conditions are essential for creating a strong and stable plaster for printmaking. By carefully controlling the drying process, printmakers can ensure that their plasters are durable enough to withstand the pressure of printing and produce high-quality prints.
Surface preparation
In the context of “how to make a plaster for printmaking”, surface preparation is a crucial step that directly affects the quality and success of the printmaking process. The plaster surface must be properly prepared to ensure that it is smooth, receptive to printing ink, and capable of transferring the desired design onto paper or other printing materials.
Sanding is a common surface preparation technique used to smooth out any imperfections or rough spots on the plaster surface. This process helps to create a more even and consistent surface, which is essential for achieving high-quality prints. Sanding can be done manually using sandpaper or with the aid of power tools such as orbital sanders.
Other surface preparation treatments may include applying gesso or other primers to the plaster surface. These treatments can help to seal the surface, improve its receptiveness to ink, and prevent the absorption of moisture, which can affect the print quality. The specific surface preparation techniques used will depend on the type of printmaking technique being employed and the desired artistic.
Understanding the importance of surface preparation and employing the appropriate techniques are essential for creating a plaster surface that is suitable for printmaking. By carefully preparing the plaster surface, printmakers can ensure that their prints are sharp, detailed, and of the highest quality.
Printing
In the context of “how to make a plaster for printmaking”, understanding the connection between printing technique and the specific requirements for the plaster surface is crucial for creating successful prints. The choice of printing technique directly influences the surface preparation and the overall process of making the plaster.
For instance, intaglio printing techniques, such as engraving or etching, require a smooth and receptive plaster surface that can hold the ink in the recessed areas of the design. This necessitates careful sanding and polishing of the plaster surface to create a uniform and non-porous surface. The plaster must also be strong enough to withstand the pressure of the printing press without cracking or warping.
On the other hand, relief printing techniques, such as woodcut or linocut, require a plaster surface with a raised design that can transfer the ink to paper. In this case, the plaster surface is carved or sculpted to create the desired design, and the raised areas are inked and printed. The plaster must be able to hold the ink on the raised areas without smudging or spreading, and it must be able to withstand the pressure of the printing press without collapsing.
Therefore, the choice of printing technique dictates the specific requirements for the plaster surface, and understanding this connection is essential for printmakers to achieve high-quality prints. By tailoring the plaster surface to the specific needs of the printing technique, printmakers can ensure that their plasters are suitable for the intended purpose and capable of producing sharp, detailed, and visually appealing prints.
FAQs on How to Make a Plaster for Printmaking
This section addresses commonly asked questions and misconceptions surrounding the process of making a plaster for printmaking. These FAQs aim to provide clear and informative answers, helping readers gain a deeper understanding of the topic.
Question 1: What type of plaster is best for printmaking?
For printmaking, it is recommended to use a high-quality plaster specifically designed for artistic purposes. This type of plaster is typically made from gypsum and has a fine grain, resulting in a smooth and durable surface. It is important to avoid using construction-grade plaster, as it may contain impurities and is not suitable for printmaking.
Question 2: What is the ideal ratio of plaster powder to water?
The ideal ratio of plaster powder to water can vary slightly depending on the specific plaster being used. However, a good starting point is a 2:1 ratio by volume. This means using two parts plaster powder to one part water. It is important to mix the plaster thoroughly to ensure a smooth and lump-free consistency.
Question 3: How long should the plaster dry before printing?
The drying time for plaster can vary depending on the thickness of the plaster layer and the ambient conditions. As a general guideline, allow the plaster to dry for at least 24 hours before printing. This will ensure that the plaster is completely dry and has reached its full strength.
Question 4: Can I use sandpaper to smooth the plaster surface?
Yes, sanding the plaster surface can help to smooth out any imperfections or rough spots. Use a fine-grit sandpaper and sand gently in circular motions. Avoid sanding too aggressively, as this can weaken the plaster surface.
Question 5: What is the best way to store plaster?
Plaster should be stored in a cool, dry place away from moisture. Store the plaster in an airtight container to prevent it from absorbing moisture from the air. This will help to keep the plaster in good condition and prevent it from hardening prematurely.
Question 6: Can I reuse plaster after it has been mixed with water?
No, plaster cannot be reused once it has been mixed with water. The chemical reaction that occurs when plaster is mixed with water is irreversible, and the plaster will harden and become unusable. Therefore, it is important to mix only as much plaster as you need for your project.
These FAQs provide essential information for individuals interested in the process of making a plaster for printmaking. By understanding these key aspects, readers can ensure that they are using the appropriate materials, techniques, and precautions to create high-quality plasters for their printmaking projects.
Transition to the next article section:
Tips on Making a Plaster for Printmaking
Creating a high-quality plaster for printmaking requires attention to detail and careful execution. Here are several valuable tips to guide you through the process:
Tip 1: Choose the Right Plaster
Select a plaster specifically designed for artistic purposes, as it is formulated to provide a smooth and durable surface. Avoid using construction-grade plaster, as it may contain impurities that can compromise the quality of your print.
Tip 2: Measure Accurately
Precisely measure the plaster powder and water according to the manufacturer’s instructions. An incorrect ratio can result in a plaster that is too thick or too thin, affecting its workability and strength.
Tip 3: Mix Thoroughly
Mix the plaster and water until a smooth and lump-free consistency is achieved. Inadequate mixing can lead to weak spots or imperfections in the plaster surface.
Tip 4: Apply Evenly
When applying the plaster, use a spatula or trowel to spread it evenly over the surface. Avoid applying the plaster too thickly, as this can increase the drying time and make the plaster more prone to cracking.
Tip 5: Allow Sufficient Drying Time
Plaster requires adequate time to dry thoroughly before printing. Allow the plaster to dry for at least 24 hours in a well-ventilated area. Rushing the drying process can result in a weak and unstable plaster.
Tip 6: Sand the Surface
Once the plaster is completely dry, lightly sand the surface using fine-grit sandpaper. This will remove any imperfections or rough spots, creating a smooth and receptive surface for printing.
Tip 7: Seal the Plaster (Optional)
To enhance the durability and moisture resistance of the plaster, you can apply a sealant after sanding. Use a sealant specifically designed for plaster, and follow the manufacturer’s instructions for application.
Tip 8: Store Properly
Store unused plaster in an airtight container in a cool and dry place. This will prevent the plaster from absorbing moisture and hardening prematurely.
By following these tips, you can create high-quality plasters that will produce excellent prints and enhance your printmaking experience.
Transition to the article’s conclusion:
Conclusion
This comprehensive guide has explored the intricacies of “how to make a plaster for printmaking,” providing a detailed roadmap for aspiring and experienced printmakers alike. We have delved into the selection of appropriate materials, the crucial mixing and application techniques, as well as the importance of surface preparation and drying. Each step has been carefully explained, emphasizing the impact on the final print quality.
Understanding the art of plaster making is fundamental to successful printmaking. By mastering these techniques, printmakers can create durable and high-quality plasters that will produce exceptional prints. The key lies in meticulous attention to detail, patience, and a commitment to experimentation. As you embark on your printmaking journey, remember the principles outlined in this guide to elevate your craft and create truly captivating works of art.
Youtube Video:
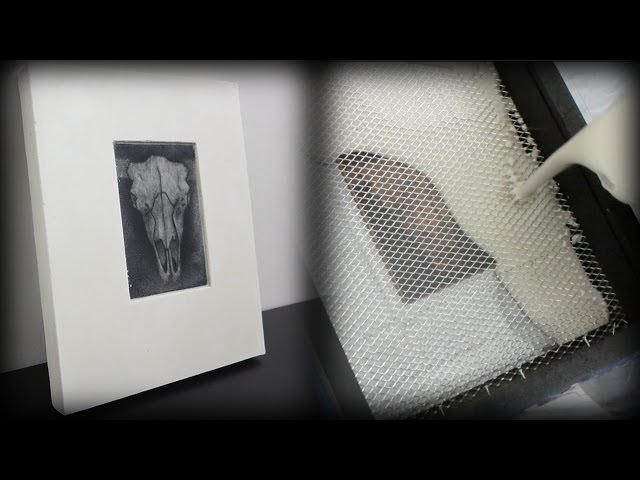